Porosity in Welding: Identifying Common Issues and Implementing Best Practices for Avoidance
Porosity in welding is a pervasive issue that frequently goes undetected till it triggers significant issues with the stability of welds. In this conversation, we will explore the vital variables contributing to porosity development, analyze its damaging results on weld efficiency, and go over the finest techniques that can be adopted to lessen porosity event in welding procedures.
Common Root Causes Of Porosity
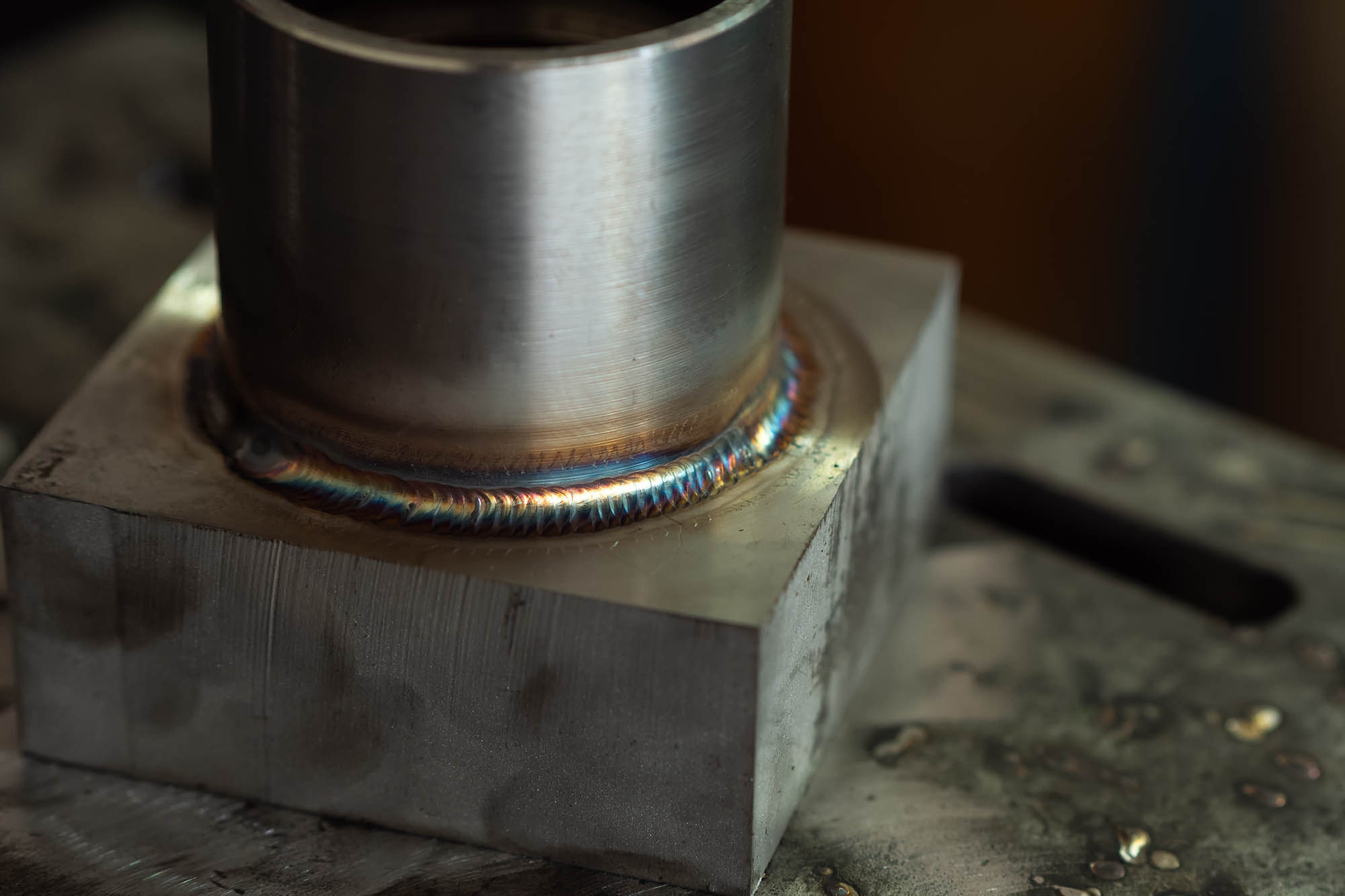
Making use of dirty or damp filler products can introduce contaminations right into the weld, contributing to porosity issues. To reduce these typical reasons of porosity, complete cleansing of base steels, correct securing gas choice, and adherence to optimum welding criteria are necessary techniques in accomplishing premium, porosity-free welds.
Impact of Porosity on Weld Top Quality

The visibility of porosity in welding can considerably compromise the architectural stability and mechanical buildings of welded joints. Porosity creates voids within the weld steel, weakening its overall strength and load-bearing capacity. These spaces act as anxiety concentration points, making the weld extra vulnerable to cracking and failing under used lots. Furthermore, porosity can reduce the weld's resistance to deterioration and various other environmental variables, even more decreasing its long life and efficiency.
Among the key repercussions of porosity is a decline in the weld's ductility and toughness. Welds with high porosity degrees tend to show lower influence strength and lowered capability to flaw plastically before fracturing. This can be specifically concerning in applications where the bonded components undergo dynamic or cyclic loading problems. Porosity can restrain the weld's capacity to properly send forces, leading to early weld failing and potential security threats in vital frameworks. What is Porosity.
Ideal Practices for Porosity Avoidance
To enhance the structural honesty and high quality of bonded joints, what particular measures can be executed to reduce the incident of porosity throughout the welding procedure? Porosity avoidance in welding is crucial to make certain the stability and strength of the last weld. One effective practice is proper cleaning of the base metal, getting rid of any type of pollutants such as corrosion, oil, paint, or dampness that can bring about gas entrapment. Ensuring that the welding tools remains in great condition, with tidy consumables and suitable gas circulation rates, can also substantially decrease porosity. In addition, preserving a stable arc and managing the welding parameters, such as voltage, present, and travel rate, helps develop a consistent weld swimming pool that minimizes the danger of gas entrapment. Using the right welding technique for the certain product being welded, such as readjusting the welding angle and gun setting, can better avoid porosity. Normal evaluation of welds and instant removal of any concerns identified during the welding procedure are essential methods to avoid porosity and produce top notch welds.
Value of Correct Welding Strategies
Applying correct welding strategies is extremely important in ensuring the structural integrity and top quality of bonded joints, building on the structure of reliable porosity avoidance procedures. Welding strategies directly affect the total strength and sturdiness of the welded structure. like this One key facet of correct welding strategies is keeping the right warm this contact form input. Excessive heat can lead to raised porosity as a result of the entrapment of gases in the weld pool. Conversely, insufficient warmth might cause insufficient combination, creating potential weak factors in the joint. Furthermore, using the appropriate welding criteria, such as voltage, present, and travel speed, is vital for attaining audio welds with marginal porosity.
Furthermore, the selection of welding process, whether it be MIG, TIG, or stick welding, need to line up with the details requirements of the task to guarantee optimum results. Appropriate cleansing and prep work of the base metal, in addition to picking the best filler product, are additionally vital parts of skilled welding strategies. By adhering to these finest techniques, welders can minimize the danger of porosity formation and create top quality, structurally sound welds.

Checking and Top Quality Control Steps
Quality control procedures play an essential function in validating the integrity and dependability of welded joints. Checking treatments are important to find and protect against porosity in welding, guaranteeing the stamina and longevity of the last product. Non-destructive testing techniques such as ultrasonic testing, radiographic screening, and aesthetic examination are typically used to recognize possible defects like porosity. These techniques enable the evaluation of weld high quality without jeopardizing the stability of the joint. What is Porosity.
Carrying out pre-weld and post-weld evaluations is additionally vital in keeping quality assurance standards. Pre-weld assessments over at this website include verifying the products, equipment setups, and tidiness of the workplace to avoid contamination. Post-weld inspections, on the various other hand, evaluate the last weld for any type of problems, including porosity, and verify that it meets defined standards. Applying a detailed quality assurance strategy that includes complete testing treatments and inspections is vital to reducing porosity concerns and ensuring the total high quality of bonded joints.
Verdict
To conclude, porosity in welding can be a common problem that influences the quality of welds. By determining the typical reasons of porosity and implementing best methods for avoidance, such as correct welding strategies and screening measures, welders can guarantee excellent quality and trusted welds. It is essential to prioritize avoidance methods to reduce the incident of porosity and preserve the stability of bonded frameworks.